Si inizia con il solito scarico “aperto”, con un kit di getti o una centralina per dare più benzina al motore: tuttavia, spesso la ricerca di cavalli e prestazioni da parte dell’appassionato non si ferma a questo livello base.
Quando s’inizia a mettere mano seriamente alla parte termica, si arriva quasi subito a parlare della sostituzione dei pistoni e delle bielle. Queste ultime in particolare, fatte salve le caratteristiche geometriche, vengono rimpiazzate con altre di materiale ben più pregiato rispetto all’acciaio di serie, vale a dire il tanto desiderato titanio.
In Ducati, questi raffinati componenti sono stati negli anni ad appannaggio dei soli modelli di punta della famiglia Superbike e ciò ha costituito da sempre un innegabile richiamo di pregio per l’intera produzione bolognese.
Un tempo associato esclusivamente a progetti aeronautici e aerospaziali, oggi il titanio, grazie alla migliorata tecnologia estrattiva e produttiva, è divenuto un materiale relativamente accessibile, specie per la minuteria meccanica, come viti, perni e boccole.
Certo, il costo di prodotti semifiniti è ancora molto alto se paragonato a quello, irrisorio, degli acciai e a quello, piuttosto contenuto, delle leghe leggere di uso comune; è palese, però, come, in un futuro non troppo lontano, la sua applicazione all’industria motoristica andrà sempre più generalizzandosi.
Rispetto ai sopra citati comuni materiali strutturali, le leghe di titanio offrono un rapporto prestazioni/peso assai favorevole, in particolare per quanto riguarda la resistenza a trazione, comparabile a quella di un acciaio di tipo comune, il cui peso è però superiore fino al 70% (dunque molto vicino al doppio). Ovviamente, è impietoso il confronto in termini di robustezza con le normali leghe leggere di alluminio o magnesio, la cui resistenza strutturale è già parecchio inferiore al peggiore degli acciai (il peso del titanio resta comunque appena superiore).
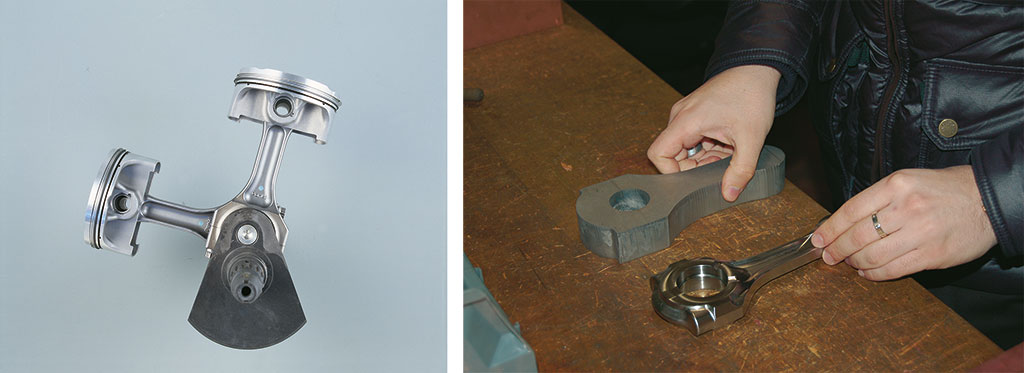
Entrando nello specifico, le proprietà essenziali della lega più usata (Ti-6Al-4V) sono confrontabili con quelle di un acciaio trattato termicamente ad altissima resistenza (34CrMo4, di tipo similare a quello adoperato per i tralicci Ducati), con quelle delle leghe di alluminio, zinco e magnesio ad alta resistenza (Al 7075) e con quelle della lega di magnesio forgiata, ad alta resistenza (AZ80).
Da quanto si è appena detto si capisce come le leghe di titanio possano rimpiazzare gli analoghi componenti in acciaio senza grosse modifiche progettuali in termini di dimensioni e forma, laddove con le leghe leggere occorre invece un apprezzabile sovradimensionamento: fatto di cruciale importanza nel campo delle due ruote, dove leggerezza e compattezza sono sempre due parametri imprescindibili.
Il metallo delle meraviglie, a parte il costo, ha poche controindicazioni: il suo comportamento a fatica e a rottura è ottimo, mentre la resistenza alla corrosione è fenomenale (paragonabile a quella dell’acciaio inossidabile, per rendere l’idea).
Bene, se a questo punto si può ben comprendere il vantaggio in termini di peso e resistenza del costruire qualcosa in titanio, qual è la reale influenza sul rendimento del motore da parte di una coppia di bielle così pregiate? Vale veramente la pena di imbarcarsi in tale dispendiosa operazione per migliorare le prestazioni del nostro motore?
La risposta è presto trovata.
La funzione “cinematica” della biella è semplicemente quella di collegare il pistone con l’albero motore, consentendo di imprimere a quest’ultimo l’energia sviluppata dalla combustione e, nel contempo, muovendo il pistone per inerzia verso la successiva fase utile. Viene identificato quale “piede” di biella l’estremità piccola in cui viene inserito lo spinotto del pistone (dunque la parte superiore), mentre per “testa” si intende l’estremità più grande, su cui si impegna il perno dell’albero motore. I vincoli sono agevolati dalla presenza di bronzine o cuscinetti a rotolamento.
Il “fusto” della biella, ovvero la parte centrale, ha solitamente sezione ad “H” o ad “I”, a seconda dell’orientamento rispetto al piano di rotazione.
Mentre nei motori a 2 tempi la biella è quasi sempre monolitica, nei 4 tempi, come i bicilindrici Ducati, la testa di biella è scomponibile grazie a un “cappello” unito tramite bulloni passanti o mordenti.
Dal punto di vista “dinamico”, la biella è uno degli elementi più stressati in un motore ad elevate prestazioni, a causa soprattutto delle elevate forze di pressione che si generano in camera di combustione e delle forze d’inerzia, particolarmente incisive nei bicilindrici di grossa cubatura (dove giocoforza i pistoni e lo stesso manovellismo hanno masse rilevanti), in special modo agli alti regimi di rotazione.
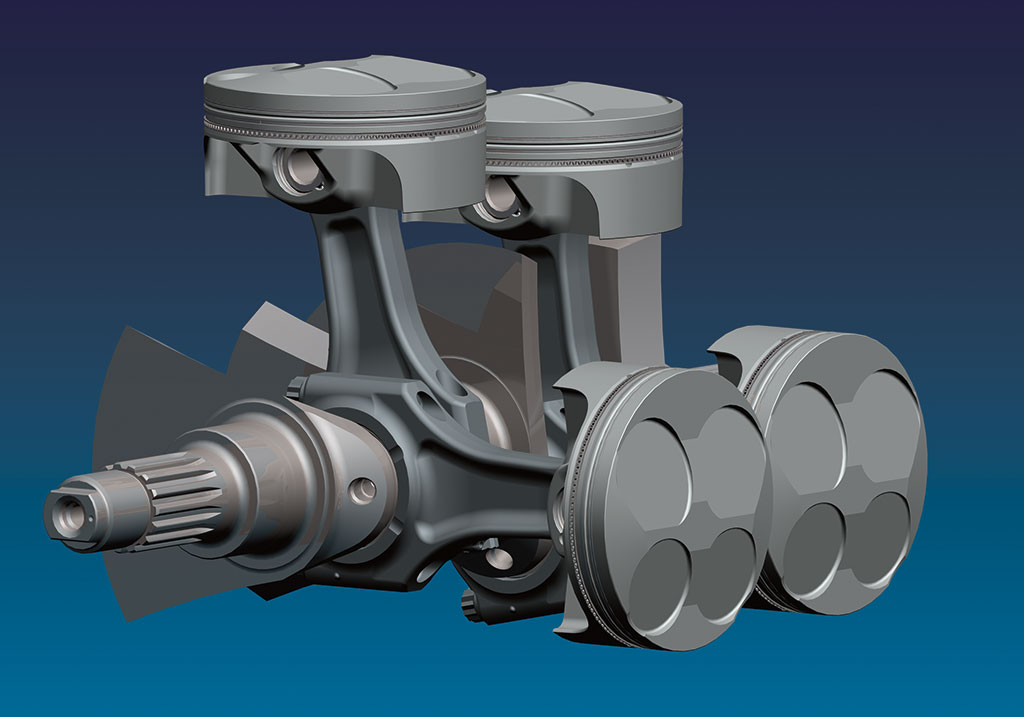
I carichi sono di tipo rapidamente variabile nel tempo e consistono in un’alternanza di compressioni e trazioni, senza trascurare una componente flessionale dovuta al particolare movimento della manovella. Quest’ultimo, poi, fa sì che solo un terzo della massa delle bielle sia da considerarsi quale massa oscillante.
Il ricorso a leghe leggere di alluminio, pur riservato ad applicazioni particolari, è chiaramente da scartare nella stragrande maggioranza dei casi, date le scadenti caratteristiche strutturali di questi materiali. Il titanio, invece, grazie alle sue qualità di robustezza, ben si adatta al gravoso compito.
La minore inerzia, derivante dal risparmio di peso (mediamente attorno al 40%), consente un innalzamento dei limiti di rotazione del motore piuttosto considerevole, ovvero fino a 1000 giri in più rispetto ai migliori acciai, su motori da competizione; il tutto senza variazioni in termini di affidabilità.
Come insegna la matematica, l’aumento del regime di rotazione, tra l’altro aiutato dalla riduzione delle perdite per attrito interno, consente di raggiungere picchi di potenza più elevati.
Inoltre, ovviamente, ad ogni apertura del gas il motore è più reattivo e rapido nel salire di giri.
Per le stesse motivazioni, non bisogna dimenticare come montando le bielle in titanio sia raccomandabile effettuare una nuova equilibratura dell’albero motore.
Rispetto ad altri componenti usualmente realizzati in titanio (come le valvole di scarico), i problemi di usura delle parti in strisciamento e le sollecitazioni termiche sono relativamente meno critici, grazie all’interposizione delle bronzine o dei cuscinetti su testa e piede di biella, nonché alla relativa “lontananza” dalle zone più calde (camera di combustione e condotti di scarico).
Nonostante ciò, la ridotta resistenza all’usura del raffinato metallo (rispetto all’acciaio) rende necessarie particolari attenzioni alla finitura e alla protezione delle superfici di lavoro.
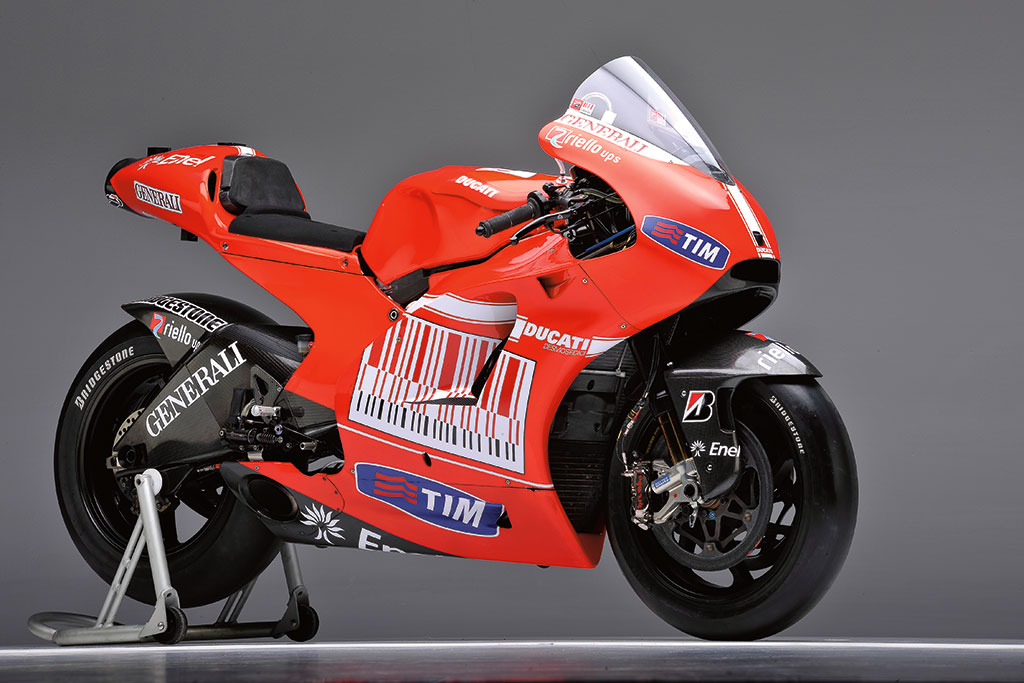
A questo proposito, non si può trascurare come le bronzine lavorino efficacemente solo in condizioni di lubrificazione idrodinamica, ovvero quando il tutto è già in movimento.
Nella fase di avvio, la lubrificazione è di fatto quasi nulla e le superfici sono a diretto contatto, il che può facilmente indurre fenomeni di intensa usura adesiva (fatali per il titanio non trattato).
I rivestimenti di protezione sono generalmente a base di fosforo, bronzo o molibdeno: ogni costruttore opta per soluzioni personalizzate (sulle bielle Ducati, a tal proposito, è stato adottato un riporto in PVD-CrN) e ultimamente si sta generalizzando l’uso di riporti al TiN (nitruro di titanio), cioè dello stesso tipo ormai divenuto standard per gli steli delle forcelle upsidedown.
La produzione delle bielle in titanio avviene nella quasi totalità dei casi per forgiatura: il metallo è portato ad alta temperatura (circa 1000 °C) e “plasmato” nella forma da uno stampo movimentato da una pressa, con più passate successive.
Solo per applicazioni artigianali, o particolarmente raffinate, si ricorre alla cosiddetta produzione “dal pieno”, ovvero per lavorazione meccanica (fresatura a controllo numerico) a partire da un blocco di metallo integro.
Come detto, la lega di maggiore utilizzo è denominata Ti-6Al-4V (lega “workhorse” per uso generico e ad alta resistenza), ma ultimamente sono state introdotte composizioni più economiche come la Ti-6Al-l1.7Fe-1Si (Timetal®62S) e la Ti-4.5Al-3V-2Mo-2Fe (SP 700).
Come si nota, tutti questi composti contengono sempre alluminio e additivi metallici (silicio, vanadio, ecc..) volti a migliorare le caratteristiche meccaniche e di affidabilità.
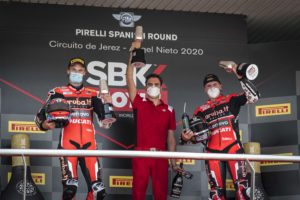
SBK a Jerez: avanti tutta!
A Jerez de la Frontera, seconda tappa del campionato SBK, si ri-accende lo spettacolo con Ducati protagonista. Doppietta di Redding e secondo posto in gara 2 per Davies.
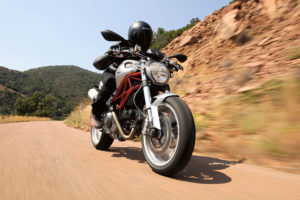
Come realizzare una batteria superleggera senza spendere una follia
Come realizzare una batteria per moto superleggera, ed anche più piccola negli ingombri, senza spendere una follia.